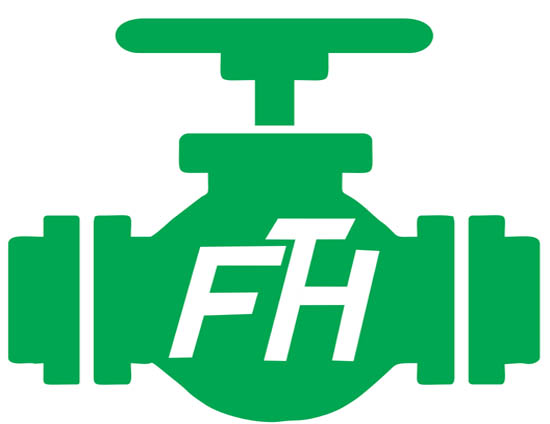
VALVE INSTALLATION
Ball Valve
When operating on a valve, do observe basic safety protocols.
Before mounting the regulator, flush the pipeline. Weld spatters, welding sticks, rocks, equipment, and other debris left in the pipeline will destroy the valve.
After installing the valve, cycle it three times and re-torque the bolts as required.
Gate Valve
When operating on a valve, do observe basic safety protocols.
With the wedge in the completely closed state, the valve should be welded into the line. Also partly opening the valve will result in distortion and leakage.
Check the sketches to ensure that the valve is capable of bi-directional sealing. If the valve will only seal in one direction, make sure it is mounted in the pipeline in the proper orientation.
On the side of single-direction sealing gate valves is a nameplate with a relief hole or pressure equaliser. When the valve is locked, this should be the high pressure foot.
Globe Valve
When operating on a valve, do observe basic safety protocols.
In most cases, the inlet of a globe valve should be mounted below the valve seat. The valve can be mounted so that the flow enters over the top of the seat and flows down into it for extreme throttling operation. The packings would be continuously pressurised in this arrangement. Check with FTH TUBES AND VALVES if the valve would be used in close proximity to throttling.Throttling operation is not ideal for globe valves per seat.
With the disc in the completely closed state, the valve should be welded into the line. And leaving it partly open will result in distortion and leakage. Allow for cooling of the weld before using the valve for the first time in the pipeline.
A globe valve's desired position is upright. Other orientations for the valve are possible, but any deviation from vertical is a compromise. It is not advisable to instal the bonnet upside down so soil can collect.
Check Valve
When operating on a valve, do observe basic safety protocols.
Check valves must be mounted such that the arrow on the valve's body points in the correct fluid flow path.
Upstream pumps, elbows, fittings, and appliances should be at least ten pipe diameters apart from all check valves.
FTH Tubes and Valves Without springs, search valves should be mounted with the bonnet up and the angle of incline should not exceed 45 degrees from horizontal. The valve bonnet can also have a roll angle of no more than 45 degrees from side to side.
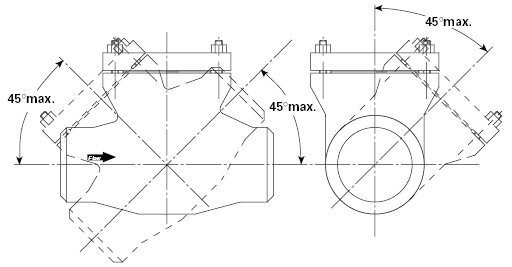
If vertical installation of a tilting check valve was not specified during the quotation point, special disc machining is needed.
FTH TUBES AND VALVES should be tested. Engineering to see how the flow satisfies the valve's minimum flow conditions. Low flows can result in disc chatter, seat and disc wear, and erosion.
To avoid slang due to an inadvertent pump trip, check valves in several pump circuits can require special designs. Pump coast-down features, verfiy flows To guarantee trouble-free operation, consult FTH TUBES AND VALVES.
For butt weld end valves
Ascertain that the valve is in the open position and that a proper spatter guard is applied to the inside of the valve body/body end's body bore.
The heat treatment applied after the weld must be localised. Make sure the valve's key section isn't exposed to excessive heat (seats and ball). Valve should not be covered by stress reliever blankets. The main body part should not be hotter than the rated valve temperature.
Because of contractor heat treatment orders, it could be appropriate to delete all internal 'soft' content in some applications.
Automation by a third party When automating FTH Tubes and Valves Ball valves in the sector, FTH Tubes and Valves advises following comprehensive procedures. For these operations, please contact FTH Tubes and Valves.
Butterfly Valve
Butterfly valves should have their valve shafts mounted horizontally or slightly inclined from vertical.
The valve should be installed with the 'HP' label in the desired direction.
For working temperatures above 392F, thermal insulation of the valve body is recommended (200C).
To avoid damaging the laminated seal in the disc during installation, the valve should be mounted in the closed spot.
Make sure the valve disc should not come into contact with the pipe lining during the opening stroke if the pipe is lined. The valve disc will be damaged if it comes into contact with the lining.
When automating FTH Tubes and Valves Butterfly valves in the sector, third-party automation FTH Tubes and Valves. recommends specific procedures. For these operations, please contact FTH Tubes and Valves.
.
.